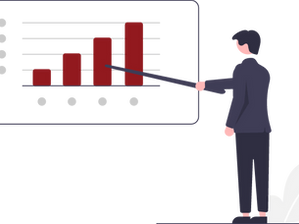
How to Run a Productive Kaizen Event for Your Business: A Guide
Have you ever looked at your workplace and thought, ‘Wow, this place could really use some improvement’? Well, you’re not alone.
In fact, it’s a common sentiment among employees everywhere. And while we can’t guarantee that a Kaizen Event will turn your office into a futuristic utopia complete with hoverboards and robot assistants, we can promise that it will make a significant difference in the way things are done.
So grab your hard hat and tool belt, because we’re about to give you the inside scoop on how to run a successful Kaizen Event.
Ready? Let’s go.
What is Kaizen?
Kaizen is a Japanese word that means “continuous improvement.” It’s a way of thinking that encourages everyone in an organization to look for small ways to make things better every day. The idea is that by making small changes over time, you can achieve big improvements.
So a kaizen event is basically a brainstorming session where everyone in an organization comes together to discuss ideas for how to make things better. It’s an opportunity for the whole team to get creative on eliminating waste, streamlining processes, and improving customer service.
When to hold a kaizen event
Ideally, you should hold a kaizen event at least once a quarter. This will give your team time to come up with new ideas and put them into action before the next event.
Here are some specific scenarios where companies could use a kaizen event:
You want to improve software testing: If your team is struggling with testing processes, a Kaizen event could be a great way to make things better. Together, you could brainstorm ideas to streamline the testing process, automate testing, or try new testing tools and techniques to improve the overall quality of your software.
You want to reduce cycle time: Is your development process taking longer than you’d like? Holding a Kaizen event could help you identify and eliminate bottlenecks, simplify workflows, and reduce wait times. By working together, you could find ways to make your development process faster and more efficient.
You need to improve communication and collaboration: If your team is having trouble communicating effectively, a Kaizen event could help you work better together. You could explore new communication tools and techniques, such as daily stand-ups or virtual collaboration tools, to make it easier for everyone to share information and work together.
You’re sick of defects and bugs: No one likes dealing with bugs and defects in their software. A Kaizen event could be a great way to identify and eliminate issues with your code. Together, you could brainstorm new software development practices, such as test-driven development or code reviews, to improve the overall quality of your code and reduce the number of bugs and defects.
You’re looking to deploy new development methodologies: A Kaizen event could help you successfully transition to a new way of working, like agile or lean development. Together, you could develop new processes, tools, and techniques to support the new methodology and ensure a successful transition.
Overall, Kaizen events are all about bringing your team together to identify areas for improvement and work together to make things better. By making small, incremental changes, you can improve the quality, efficiency, and collaboration of your software development process.
Before the Kaizen event: How to prepare for your meeting
For a truly successful Kaizen event, you need to be prepared.
Here’s what that looks like:
Have a discussion with the sponsor who holds the authority to implement improvements and remove obstacles (e.g., company owner, plant manager, or functional manager). During this conversation, it’s crucial to define the event’s purpose, scope, deliverables, and agenda in order to establish clear goals and expectations for the project.
Assemble a Kaizen team with a mix of those who do the job, supervisors, and technical resources like developers, QA engineers, and product owners. The team should be scheduled to meet at least one week in advance.
Coordinate the room and timing of the event with all participants. A one-page event description should be discussed with everyone to ensure they understand the purpose and process.
Brief employees not directly involved in the Kaizen event on its purpose and process, and when they will have the opportunity for input – like during a trial and/or review conducted before kaizen changes become standard procedures.
Review the agenda, define kaizen and lean production in your own words, give specific examples of the seven kinds of waste, and prepare for anticipated questions or resistance to change.
Use paper, sticky notes, whiteboards, or online co-editing applications like Google Docs or Microsoft Word to capture ideas that will be discussed during the event.
Following these steps ensures that your Kaizen event runs as smoothly and productively as possible. Now, let’s move on to what happens during the event itself.
You’ll want to break the Kaizen event down into multiple sessions:
Session 1: Your team will identify wastes and develop ideas for improvement.
Session 2+: Your team will assess how well the improved process is working and establish a standardized workflow if the system works.
Session 1: Finding chinks in the armor
Phase 1: Open the meeting
To kick off your kaizen event, start with introductions and ask if anyone has prior experience in kaizen, lean, or lean six-sigma. Give a brief overview if necessary. Then, have the sponsor introduce the event’s purpose and desired outcomes.
Finally, review the 7 types of waste and ask for examples. When everyone’s ready, begin the waste walk.
Phase 2: Go through the waste walk
The waste walk is a team activity that helps identify waste in the workplace, which could be lost time, materials movement, or any other non-value-adding activity.
During the waste walk, the team divides into pairs or trios armed with a clipboard or tablet to observe and list any wasteful activities in the workplace. You can ask how job holders do their tasks (if it has been approved by the local area supervisor). Just remember that you’re not discussing solutions right now, only slow-moving processes and problems.
Pro tip: Use the “5 whys” technique to get to the root cause of any issue you uncover. The idea is to ask “why” five times, to drill down to the underlying issue causing the waste. For example, your team might notice that employees are spending too much time searching for tools.
They will ask “why” they waste time searching for tools.
The answer may be that the tools are not organized, so they will ask “why” again.
The answer may be that there is no designated tool storage area, so they will ask “why” once more.
After asking “why” five times, they will identify the root cause of the waste, which may be that there are no standard procedures for tool storage.
Related: How to Identify Inefficiencies in a Software Development Process: 9 Hallmarks + Fixes
(Example) The time CyberMedics went on a waste walk with Collins Aerospace
Collins Aerospace, a supplier of aerospace and defense products, was struggling with expired materials on the assembly floor, which led to a failed AS9100 audit. When they reached out to CyberMedics for help, we conducted in-person kaizen events to identify the root cause of their materials management problem.
Our team found that their existing process was no longer sustainable for their growing workload and relied heavily on a single person to manually track all materials with an expiration date. To address this issue, we developed a new system that included:
Auto-escalating notifications for upcoming expirations
Easy-to-use digital material location tracking
Seamless integration into their existing inventory system
After rolling out the new system in a gradual approach, we trained the technicians on the new process to ensure a smooth transition. We then analyzed the impact of the new system and developed reports to help management identify process failures. With the new system, the responsibility for quality compliance was spread throughout the organization. Our approach not only addressed their immediate issue but also helped them establish a more sustainable process for their future growth.
Phase 3: Talk, prioritize, and group wastes
Once the waste walk is completed, the team should regroup in the conference room or online meeting to discuss and group the identified wastes. To ensure everyone is on the same page, it’s helpful to include the initials of the author on each note. Then, under the broad headings of “people”, “process”, and “tools/systems”, the team leader should work with the team to group these notes.
If there are any notes that don’t fit the scope of the kaizen event, like policy issues or new equipment, they can be added to a “parking lot” to avoid distraction and keep the team focused on the main topic.
Pro tip: Use dot voting to prioritize tasks as a team
Dot voting is a quick and easy way to determine the most important items on a list. Participants are given a fixed number of dots to place next to the items they think are most important (everyone votes at once). This allows people to vote for multiple options and reveal relative priorities instead of having just one winner. After all the dots are placed, the leader counts them to identify the preferred options.
Typically, each person is given enough dots to vote on multiple items, and the number of allowed votes should be no more than 30% of the available options. Many teams use 3 dots per participant every time to keep it simple.
Phase 4: Time to brainstorm solutions
When the waste walk and prioritization are complete, it’s time to move on to brainstorming.
The team leader should create an engaging environment where ideas are encouraged. Start with a blank slate and don’t limit yourself with preconceived ideas or assumptions. Make sure everyone has an opportunity to input their thoughts, even if they initially seem far-fetched.
Brainstorming should be a continuous cycle of questioning, envisioning potential solutions, and challenging the status quo. To generate ideas, use the “5 Whys”, root cause analysis, or any other technique that works for your team.
Related: 4 Types of Business Process Automation: Examples + Setup guide
Once the brainstorming is complete, it’s time to move on to experimentation.
Phase 5: Planning the kaizen experiments
After the team has identified preferred solutions and countermeasures for the waste, the next step is to plan the kaizen experiments. This is where the team defines a way to trial run the proposed kaizen ideas for a few minutes, hours, or a day to observe how well they work.
During the planning stage, it’s important to ensure that team members are present to observe the trial runs and ask for additional input from other employees. The experiments should be clearly defined, and action items should be created for each experiment, assigning an owner and setting a due date for completion.
Phase 6: Wrapping the kaizen meeting up
As the kaizen event comes to a close, conduct a final review of the process and next steps. Take a moment to revisit the parking lot items to clarify any lingering questions and assign individuals to follow up on them with the sponsor after the meeting. Make sure everyone is on the same page and committed to their action items, and express gratitude for their participation in the kaizen event.
Remember to encourage ongoing communication and collaboration among team members to ensure the success of the kaizen process. With a solid plan and a team that is committed to continuous improvement, the organization can look forward to increased efficiency, reduced waste, and better results overall.
What to do in-between meetings
Kaizen is an ongoing process that requires a commitment to continuous improvement and collaboration.
Right after the meeting: Send a follow-up email or message to the team. Include a summary of what was discussed and achieved, as well as key points that need attention before the next meeting.
Monitor progress on action items, provide feedback to the team and look for opportunities for further improvement. Encourage team members to share their ideas and solutions with each other outside of the meetings.
Meet with sponsors periodically to review and discuss progress on key projects. Keep sponsors updated on project statuses and roadblocks that need their attention, as well as any successes or breakthroughs achieved by the team.
Session 2+: Reviewing and Approval
Phase 1: Hello, again!
Welcome the team back! Before moving forward, take a moment to ensure that everyone had a chance to read the list of kaizen improvements. Once everyone is re-acquainted with the work, move to the next phase.
Phase 2: Review and approve the new process
Now that the team has validated a solution through an experiment, it’s time to write up the new standard work procedure, including a picture – this new procedure will circulate to all involved operators for final approval.
Once the team has finalized the new standard work procedure, it becomes the official process for all employees to follow. You’ll want to assign someone to distribute the new procedure to all involved operators to ensure that the kaizen improvements are put into practice – this is a critical step in implementing the changes and making them a part of the standard work process.
Of course, encourage the team to take a final look at things and review any changes that need to be made. If everyone is in agreement, then it’s time to move on to the next agenda item.
Phase 3: Planning your next Kaizen experiment
Alright, it’s time to plan your next kaizen experiment! Take a look at your list of wastes from earlier and choose another kaizen in the same area to focus on. If you’ve already addressed all the significant wastes in that area, or if a different work area or process needs the team’s attention, it’s time to plan another kaizen or lean event.
Remember, this is an iterative approach that can help you continuously improve and optimize your software development process over time – so keep applying the kaizen process to each item until you’ve addressed all the major wastes in the development process.
If you encounter a larger problem like a system or supplier issue, be prepared for a longer-term project. This might call for the involvement of a site manager or business owner to provide the necessary expertise and resources.
Phase 4: Wrap-up and closing
As the meeting comes to a close, it’s important to quickly review any remaining items on the parking lot and assign individuals to follow up with the sponsor. Next, review all action items and make sure everyone fully understands their tasks and due dates. It’s important that task owners are committed to completing their tasks on time.
Lastly, express gratitude to everyone for their participation and contributions to the kaizen event. Thank them for their hard work and collaboration in making the process better. With that, the meeting comes to an end, but the kaizen journey continues until the next meeting. Keep up the good work!
10 best practices for a productive Kaizen event
Keep an open mind and be willing to change.
Maintain a positive attitude and be supportive of others.
Create an environment where people feel comfortable speaking up without fear of blame.
Encourage nonjudgmental thinking and be open to considering multiple alternatives.
Treat others the way you would like to be treated and respect all team members.
Every team member’s opinion counts, so ignore position or rank and create a team environment where everyone’s ideas are valued.
Don’t be afraid to ask questions or share your ideas, there’s no such thing as a dumb question.
Don’t just talk about it, take action and create a bias for action.
Prioritize creativity over capital and try to come up with innovative solutions without worrying about the cost.
Never leave in silent disagreement.
And finally, have fun! A positive, enjoyable atmosphere can help boost creativity and productivity.
Run game-changing Kaizen events with CyberMedics by your side
Running a kaizen event can be daunting, but with the right team and resources by your side, you’ll soon be rolling out changes to make processes more efficient.
At CyberMedics, we have years of experience helping teams implement lean principles in their organizations through our consultancy services – from pre-event planning, to post-event analytics. We can help you create an action plan to identify and address wastes, provide process improvement guidance, and even conduct kaizen events with our experienced facilitators.
Our goal is to help you achieve sustainable results that benefit the entire organization.
So get in touch today and see how we can work together to make your team more productive.